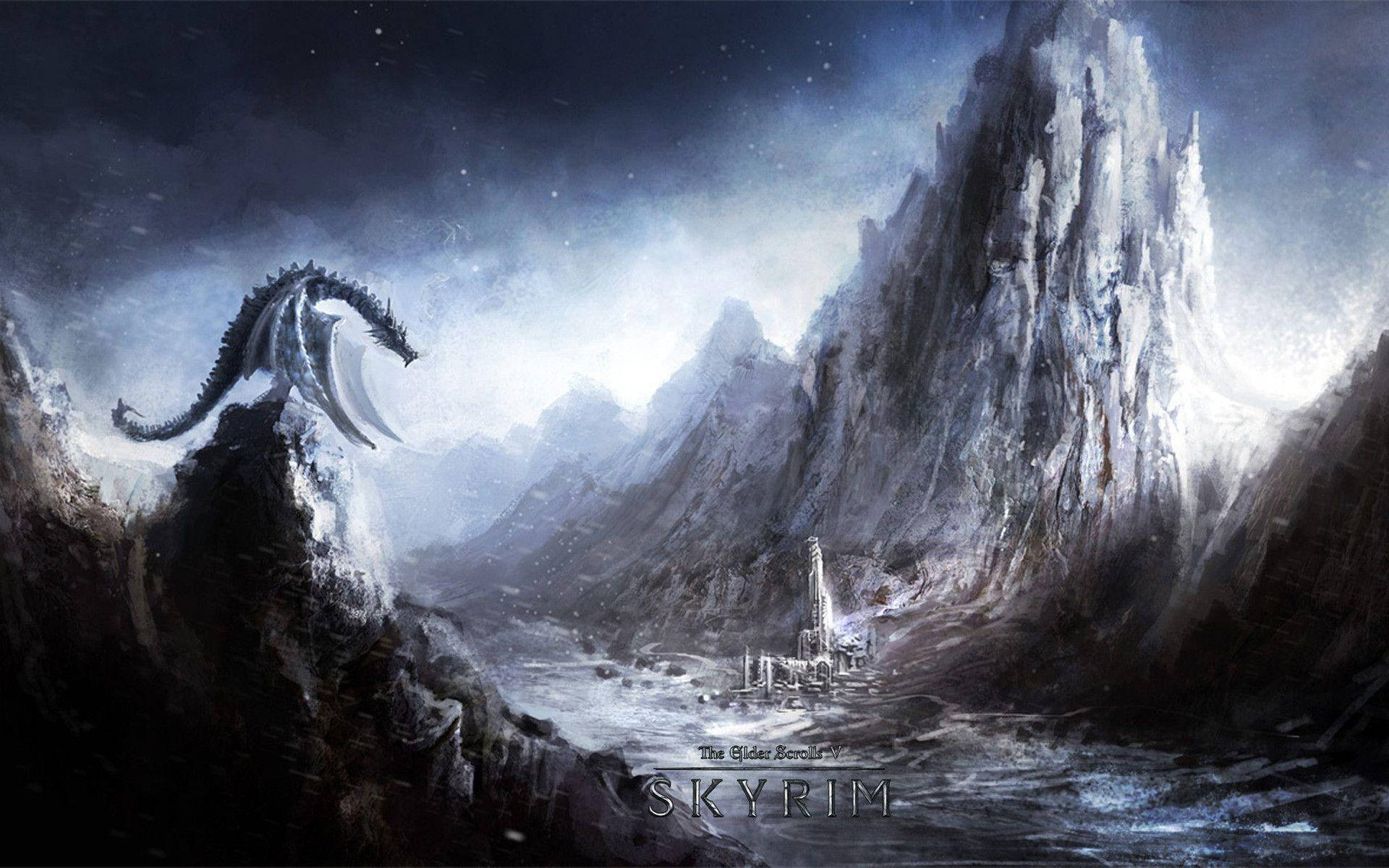
This is a series of 1920X1200 backgrounds and wallpapers that is 100% free to download. We hope that you will enjoy this collection of high definition (HD) 1920X1200 backgrounds and wallpapers, and that you will use them as your background on your desktop or home screen for your mobile.